HVAC System Replacements
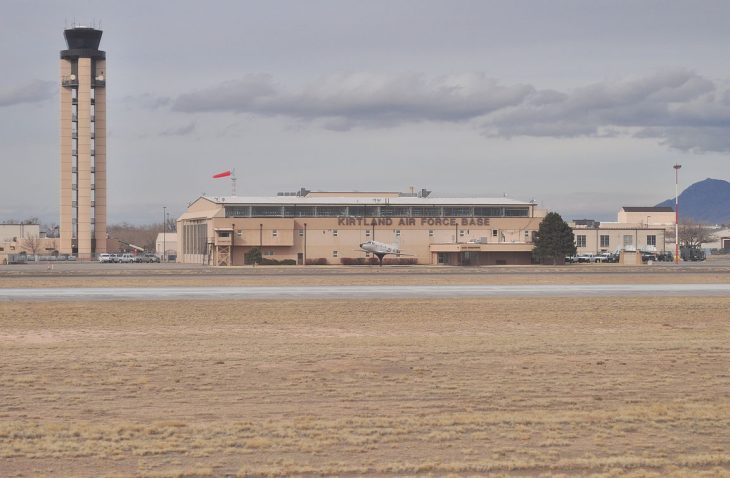
IMEG, under its joint-venture with PRIME AE, provided structural, mechanical, electrical, and plumbing engineering design services to replace the HVAC systems of Islands A, B, and C and meet the needs of the island occupants located inside Hangar 1001 at Kirtland Air Force Base. Constructed in the early 1950s, Hangar 1001 primarily houses and maintains Air Force helicopters. Located inside the hangar are three structures referred to as Island A, B, and C, which are composed of offices and industrial workspaces. Phasing was a critical part of the design and construction to upgrade the HVAC systems.
HVAC Systems – Building C
- Area 1, housing welding/water jet shops, was provided with a new packaged heat pump system with hot gas
re-heat for dehumidification including a new duct work system. - Area 2, housing breakroom/moral room, and Area 4 containing the sheet metal shop, were provided with new rooftop DX/gas-fired packaged AC units with hot gas re-heat for dehumidification. Existing duct work was modified and added to as required to accommodate the new rooftop units.
- Area 3 with first floor offices, and Area 7 with second floor offices, were provided new VRF systems with the condensing units mounted on the exterior roof of Building C.
- In Area 5, the new HVAC system was provided with new controls. The system was tested and balanced and re-commissioned as a part of this project.
- Area 6, housing the machine shop, was provided with a new split system heat pump. The existing duct work system was modified as required to accommodate the new air handler installation.
Outside Air
- Areas 1 and 6 systems received outside air via wall louvers ducted directly to each unit.
- Areas 2 and 4 roof-mounted packaged DX systems received outside air via unit mounted intakes.
- Areas 3 and 7 with VRF systems are served by a dedicated outside air (DOAS) unit mounted on the roof of Building C. Outside air is ducted to each space served by the VRF systems as required by ASHRAE 62.1.
All new supply and outside air ductwork are single wall round or rectangular galvanized duct. The facility was provided with fully ducted supply, return, exhaust, and outside air systems. New gas fired industrial unit heaters were provided for the hangar bays. A new, complete BACnet automatic temperature control system was provided for the facility. A life cycle cost analysis was completed for three alternative systems.
Five new roof top mechanical units were installed on the lean-to structure. The roof top mechanical units are supported on mechanical curbs placed on the existing four-inch deep, 18-gauge metal roof deck. New roof framing was installed under the roof deck to support the new mechanical equipment.
Modifications to the existing fire sprinkler systems were required to support the HVAC upgrades. A new fire alarm control panel was installed to serve as the building’s main control panel. New fire alarm detection and control devices were also provided to support the project HVAC replacement/upgrade.
Modifications to the existing electrical systems were required to support installation and demolition of proposed HVAC systems. Existing primary and secondary electrical distribution equipment remained and was reused. New electrical panelboards and transformers were provided and connected to the existing systems.