New Powertrain Aircraft Component Repair Shop and Engines Assembly Shop – Phase IV
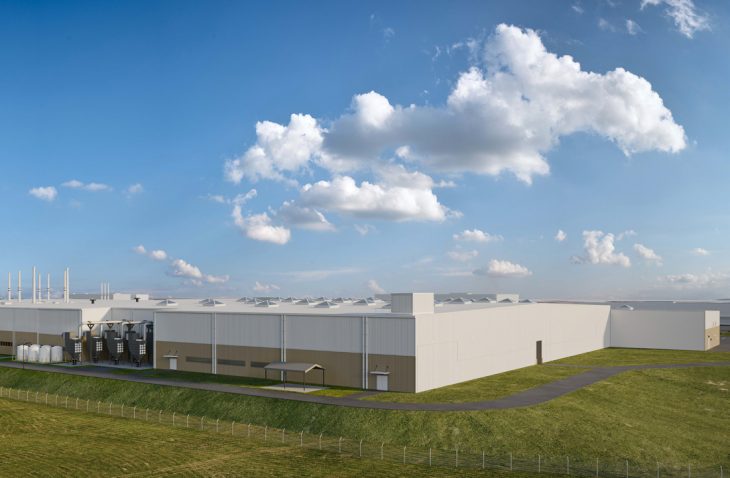
IMEG provided structural, MEP, and communications engineering design services for B1700.4, the fourth phase of the new Powertrain complex at Corpus Christi Army Depot, TX. The new ACRS Engines Assembly Shop will house the majority of repair and overhaul processes now housed in building 8, a central energy plant II, the second phase of a new administrative support facility, and related new infrastructure. The ACRS facility supports the production process and will be constructed adjacent and joined to the ACRS-Machining (Phase III, B1700.3). The building uses include helicopter assembly/disassembly, inspection, engine and component testing, welding, machining, cleaning, hydraulics, storage, and painting.
The additional central energy plant is to be constructed to house mechanical and electrical equipment. Central energy plant II (CEP II) is designed for all future expansions and is supported on shallow spread footing with a concrete slab-on-grade.
This building B1700.4 has structural steel columns supported on shallow strip and spread foundations and a reinforced concrete floor slab on grade. The lateral load-resisting system design for the building consists of structural steel braced and moment frames. The steel roof deck acts as a diaphragm. The framing system is designed in accordance with the American Institute of Steel Construction (AISC). The structure is designed to accommodate multiple 1.5-ton overhead running cranes, with a maximum of two cranes per 50-foot crane beam span.
Telecommunications rooms are provided at each side of the facility to serve the administrative areas. Cybersecurity measures are provided for the Utility Monitoring and Control System (UMCS), Fire Alarm Reporting Systems, and Electronic Security Systems (ESS), in accordance with UFC 4-010-06.
A life cycle cost analysis was conducted comparing three HVAC system alternatives. All new equipment is high efficiency, designed in compliance with ASHRAE 90.1 minimum efficiency requirements. The design includes four-pipe, hydronic, variable air volume (VAV) air handling units (AHUs). Single-zone VAV AHUs are used to condition the process floor areas and multi-zone VAV AHUs, incorporating individual zone VAV air terminal units. Air terminal units (ATU) are used to condition the support spaces. ATUs are pressure-independent, provided with hydronic heating coils, and all provided with factory-mounted electronic controls connected to the new building-wide DDC system to ensure interoperability between the new HVAC equipment and the base-wide HVAC controls integrator. The system exceeds the minimum requirement of 30% energy reduction of ASHRAE 90.1-2016.
The electrical design includes new medium voltage feeders, switchgear, substations, and connections to the new ACRS engines assembly shop. All exterior equipment is designed for use in a high-corrosion environment. Each individual functional area in the process floor area is provided with a minimum 400A, 480V, three-phase panelboard to serve the miscellaneous small 480V loads for the equipment. Power connections are provided for the new fire alarm/mass notification panel, communications equipment, security equipment, HVAC, and plumbing equipment. LED lighting fixtures are used throughout the building. A conventional lightning protection system will be provided for B1700.4, including strike termination devices, conductors, ground terminals, interconnecting conductors, surge suppression devices, and other connectors and fittings required for a complete and usable system.