From blueprints to bots, artificial intelligence is transforming advanced manufacturing
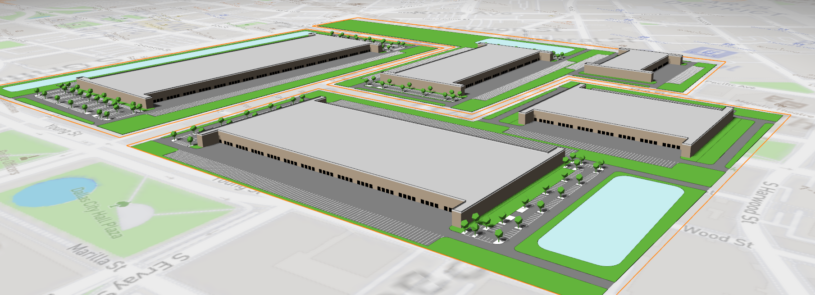
By Mike Walsh
Manufacturers have long been at the forefront of adopting automation and data-driven processes, but a new frontier is emerging that’s reshaping not just how products are made, but also where and how manufacturing happens.
That frontier is artificial intelligence.
From optimizing production schedules to forecasting energy use, AI is now playing a dual role in advanced manufacturing: enhancing operations inside the plant and shaping the design of the plant itself. AI and simulation are no longer futuristic concepts, they’re tools, and IMEG is actively integrating both into the facility design process to help clients build smarter, faster, and more resilient operations.
Improving operations
Within the manufacturing process, AI enables a level of agility and intelligence that was previously out of reach. Manufacturers are using AI to:
- Predict equipment failures before they happen, using real-time sensor data and machine learning models
- Optimize production lines by dynamically adjusting variables like speed, temperature, or batch size
- Forecast demand and supply chain disruptions, allowing for smarter inventory and logistics planning
These AI-driven insights are reducing downtime, improving quality, and making manufacturing more responsive to market shifts. To achieve these benefits, however, operational AI needs the right environment to thrive, and that starts with facility design.
Leveraging AI design tools
At IMEG, we’re bringing the AI-driven mindset to how we design the facilities that house these intelligent operations.
Take our recent use of TestFit, an AI-powered site planning tool (pictured above). For a confidential advanced manufacturing client with multiple buildings, we used the software to rapidly evaluate dozens of layout iterations in real time, factoring in everything from building footprint and adjacencies, parking needs, and zoning constraints, all anchored to the required rail. What might have taken days of manual modeling was done in minutes, enabling the project team and client to select a site layout that balanced constructability, operational efficiency, and long-term growth.
Another example: For a client exploring long-term sustainability investments, we used HOMER Energy, an AI-enabled simulation tool, to develop a 15-year capital plan for onsite renewable energy. The platform modeled various combinations of solar, wind, storage, and load shifting strategies, helping the client visualize the year-over-year impact on utility bills, carbon footprint, and payback periods.
These tools aren’t replacing engineering judgment, they’re enhancing it. AI gives us the ability to simulate complex systems, compare alternatives quickly, and validate decisions early in the design process. That’s especially powerful in a manufacturing environment where speed-to-market, resiliency, and energy performance are all mission critical.
Future-proofing investments
As more manufacturers embed AI into their processes, the demands on the facility itself are shifting. AI-ready facilities need:
- Robust digital infrastructure to support sensors, edge computing, and data analytics
- Flexible layouts to accommodate evolving workflows and automation upgrades
- Energy systems designed for insight, including real-time metering and integration with smart grids
This is where engineering meets strategy. By designing facilities with AI in mind, we’re helping manufacturers future-proof their investments and unlock greater value from their operations.
Embracing the shift
AI isn’t just about robots on the line or algorithms in the cloud. It’s about creating a smarter, more agile ecosystem, from the facility floor to the boardroom. And for those planning, designing, or operating industrial facilities, now is the time to embrace this shift.
Through the strategic use of AI and simulation, we can design facilities that aren’t just built for today’s needs, but are positioned to grow, adapt, and compete in tomorrow’s economy.