LEED Platinum Engineering Building
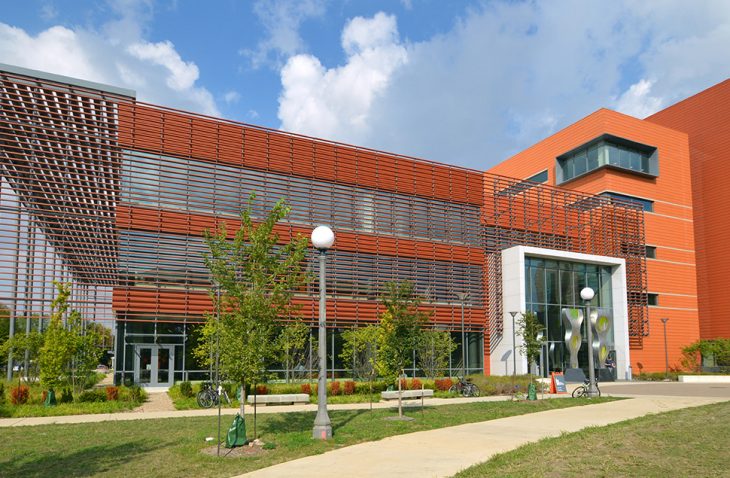
The University of Illinois’ new College of Electrical and Computer Engineering (ECE) building is the first on the university’s campus and among the first in the state to pursue a “net zero ready” design approach. The facility’s innovative design is modeled to reduce energy consumption by 50%, achieving as close to net zero as was feasibly possible for the university. The LEED Platinum facility is also on target to receive an EPA Energy Star rating of 99 on a 100-point scale.
The 230,000-square-foot facility houses high-tech instructional classrooms, 21 labs, student lounges, student organizational offices, 11 teaching assistant meeting rooms, study rooms, faculty offices, a 400-seat auditorium (one of the largest gathering spots on campus), and a nanofabrication lab with an instructional ISO Class 6 clean room.
The nanofabrication lab is the first of its kind to give undergraduate students hands-on experience with micro- and nano-electronics, providing the opportunity to work with new materials, devices, and technologies typically only available to graduate students. The lab features a dual-beam focused ion beam to be used for imaging, lithography, etching, and depositing materials; a sputtering tool for students to deposit multiple types of materials for device fabrication, and a di-electric deposition tool that allows students to work with plasma.
The 1,926-square-foot clean room (with volume of 23,112 cubic feet) includes an entry and locker room, with mechanical systems housed above. A down-flow method distributes air into the ceiling plenum, down through the clean room and perforated raised floor, and back through the service and equipment corridors. The airflow design features:
- 56,000 CFM of recirculation air
- 145 recirculation air changes available
- 9,000 CFM of make-up/pressurization air available
- 23 make-up/pressurization air changes available
- 3 levels of filtration on all airflow: 30%, 65%, and HEPA
- Acid fume hoods
- Double interlocked pre-action fire protection system
- VESDA system connected to the fire alarm system
The design also includes chilled beams, heat recovery chillers, heat recovery wheels, a water cooling loop, and high-efficiency motors that circulate air, allow for heating and cooling, transport water and steam, and power elevators. Engineers also provided design for various services including the process cooling water, exhaust, DI water, chemical fume hoods, acid waste, nitrogen, liquid nitrogen, and a miscellaneous gasses system allowing different gasses to be connected to the system depending on need.
Minimizing the facility’s carbon footprint and optimizing energy efficiency were key drivers for the University. A collaborative planning and design process – involving the architect, IMEG, and owner – involved extensive energy modeling and net zero energy analysis of innovative, alternative designs to meet the goals of the building. A computer-based energy simulation evaluated the building energy use. The energy savings were compared to a minimum code-compliant baseline building per LEED requirements. The results were compared to historical data for similar facilities to confirm the validity of the results. Numerous energy simulations and life-cycle cost analyses evaluated the various energy-saving technologies.
The design also included an owner-provided 300kW photovoltaic solar array on the rooftop, which, along with a future solar array on a nearby parking structure, will provide electricity and enable the building to reach net zero energy.