Reality Capture: The many benefits of drones and 3D laser scanners
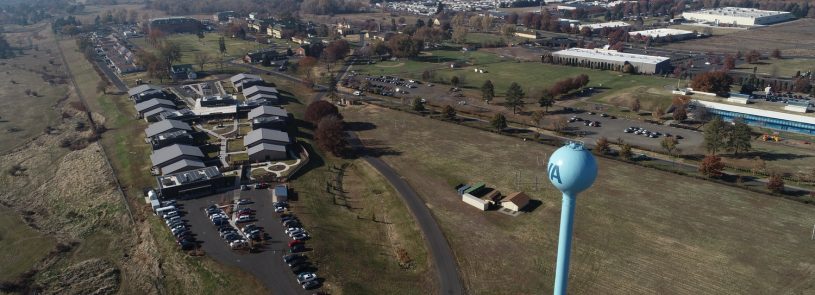
By Eric Vallejo
One of the coolest parts of my job is that I get to play with a lot of new toys – or “tools” – that are taking over the AEC industry, like drones and high-tech 3D laser scanners.
Recently, for example, I had the opportunity to create a 3D map of a large medical center in California. IMEG is providing full-service engineering and design services for the campus, so we flew one of our drones and mapped almost 200 acres in less than four hours. Farther up the coast in the Northwest, we spent several days flying our drones and conducting 3D scanning to aid in a master plan development for a Veterans Administration medical center.
Aerial imagery is nothing new, but the construction industry doesn’t benefit from photos that are static, may be 10 years old or older, and don’t capture data (e.g., Google Earth). Using a combination of state-of-the-art drone and 3D laser scanning technology, however, we can capture a current look at the actual site, the lay of the land, buildings and other structures, and collect an immense amount of data.
Before I get any deeper into what we can do with these tools, I want to cover some common terminology and details:
- Drones: An unmanned aerial vehicle (UAV) – commonly called a drone – is a component of an unmanned aircraft system (UAS), which includes a UAV, a ground-based controller, and a system of communications between the two. IMEG’s quadcopters are top-of-the line unmanned aircraft, and our pilots are certified under FAA Part 107. We can attach one of three different cameras to the drones to gather a crazy amount of information through photography and video.
- Photogrammetry: This is a rendering process that stitches together photographs captured by the drone cameras to create a continuous map or 3D model along with all associated data.
- Data points: The X, Y, and Z coordinates of any point in space based on a fixed reference location. These coordinates are the essential elements of every map or scan.
- 3D laser scanning: A process using a laser and camera set at a fixed point or points to capture measurements (data points) of exterior structures or interior spaces to create a point cloud. 3D scanners come in handheld versions, tripod/rotating versions, and total station scanners that combine high accuracy measurements using traditional survey methods with 3D laser scanning – an ideal instrument for outdoor applications.
- Point cloud: A product of the data captured by 3D laser scanners and drones. (See below.) Once data is registered and processed, it may be translated into a 3D model utilized for the basis of design, volumetric analysis (for stockpiles and quarries), or measurements – e.g., the distance and relative location between any two points, such as the distance between one utility and another, one corner of a building to another, or one end of an air handling unit to another.
As cool as all the technology is, what we can do with it is even more impressive – showing owners a flyover of their proposed or in-progress site development, creating a 3D map of large areas that would take days to map, or taking highly accurate measurements of multiple buildings on a campus. We’ve even used our 3D laser scanners to measure the surface area of a water tower so the municipality would know how much paint would be needed to repaint it.
Our drone and 3D laser scanning services are not limited to civil projects. Basically, if we can see it, we can map it, so we work closely with our other disciplines, from structural to MEP, to create some incredible, information-rich models for clients in all markets. For example, we can fly drones to provide exterior structural inspections; to provide 3D mapping of a space destined for renovation to determine where new infrastructure will fit; or scan an existing mechanical room to determine if it can accommodate the size and dimensions of a particular piece of equipment.
The uses of 3D scanners and drones are endless, especially when used together. But the best part of using these technologies is the benefit to our clients. These include:
Time savings: An area that used to take days or weeks to manually map with a GPS or a traditional survey can now be flown and mapped in hours or a few days, depending on the size of the project. Less time spent surveying at a worksite translates to cost savings for clients – and helps speed up the entire construction timeline.
Ease of access: Need to inspect the structure underneath a bridge section? No need to utilize a lift or float in on a barge. Just fly a drone.
Increased data and accuracy: The immense amount of data captured is extremely accurate and is always available for future extrapolation for other projects. Once you have a point cloud of your site, roadway, or interior space, you can reference that information forever.
Safety: Not only do these tools capture unprecedented amounts of data, they allow us to create safer work environments for our surveyors and our clients’ personnel. No one needs to venture into any potentially dangerous situation when a drone is available. (According to the blog Drone Base, of the 991 workplace fatalities that took place in the U.S. in 2016, 21% happened in construction.)
Construction industry reports and forecasts all point to the continued rise in the use of drones and 3D scanners. Considering the many benefits these technologies provide, there’s no wonder why.
Watch a 2-minute drone video that includes a 3D point cloud created from a recent VA medical center project.