Customized design is critical for every chemical and process engineering project
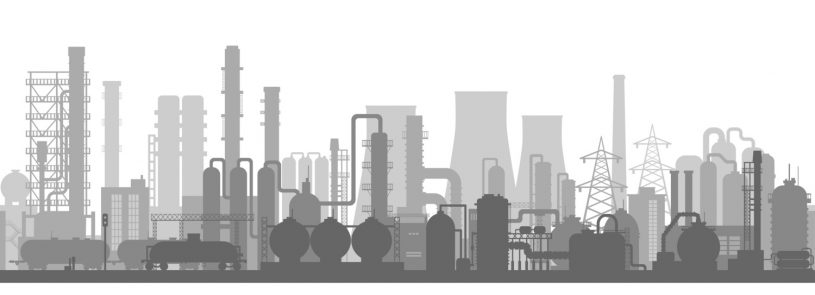
In 2020, IMEG Corp. acquired Process Results, Inc., specialists in chemical and process design. In the following Q&A, IMEG Client Executive Dale Niethammer and Project Executive D. Kevin Bingel discuss key aspects of process engineering.
Q. What is involved with chemical and process design?
A. Process engineering is the understanding and application of the fundamental principles and laws of nature that allow us to transform raw material and energy into useful products.
Chemical and process design involves the unloading, storage, transferring, mixing, reaction and possibly packaging of chemicals, chemical mixtures, or other materials in liquid, solid, or bulk forms. Each of the materials or combination of materials can be flammable, combustible, oxidizing, corrosive, abrasive, or viscous, and processed or reacted at various temperatures, pressures, vacuum, or under other special conditions. A repeatable engineering process is critical for project definition, scope development, execution, scheduling, and cost to appropriate funds and execute a project.
Each chemical and process project has unique requirements and challenges that must be resolved, so every design is typically customized for each client. Very seldom does chemical and process engineering involve repeating similar designs or processes.
Q. How do you approach process automation and control system design to ensure meeting a client’s needs and goals?
A. Process automation and control systems are defined and developed utilizing the process piping and instrument diagrams (P&ID’s) developed and approved as an integral part of the process design work. The interface between the process engineers, electrical/control engineers, and the client is critical to fully understand the process and safety requirements. A functional spec is developed as a written document to define and outline the programming requirements along with detailed interlock matrices defining all equipment and instrument control and operation. Upon client approval, systems are programmed, the program is uploaded, and a comprehensive checklist is used as part of the check-out and start-up activity. Commissioning of the system is a critical part of the work leading to final owner acceptance.
Q. What is the major goal of conducting a dust hazard analysis (DHA) as mandated by NFPA 652, and how does a facility know if it needs to conduct such an analysis?
A. In addition to being required by law, the ultimate goal of conducting a dust hazard analysis (DHA) is to keep facilities and personnel as safe as possible from potential fire or explosion caused from hazardous dust. Each facility that handles dust or creates dust in their process or has a dust collection system(s) is required to evaluate their operations for potential dust hazards. Some critical material information can be gathered from material suppliers, but often the materials/dusts need to be tested by a lab to determine if they are flammable or combustible and require a DHA. The characteristics of the dust generated, collected, or conveyed are the principal drivers that determine if a DHA is required. Facilities that do not have hazardous dusts should, at a minimum, review and document that they do not meet the threshold requirements for a DHA.
Q. You are certified to conduct insurance investigations and cost estimating for chemical or process plant accidents, explosions, fires, etc. What does this typically involve?
A. For most industrial incidents, accidents or losses, the insurance company’s needs can vary significantly. It is important for them to quickly define the cause and origin, capital losses, and business interruption costs so money can be set aside to resolve the claim or subrogate to third parties (other people, companies, or insurance carriers). Most insurance companies have an experienced team of various experts and consultants to assist, depending on need. Initial services can include Cause and Origin Investigation, definition of conceptual replacement scope/extent of loss, conceptual cost estimate for capital losses, or support of recovery/restoration contractors. Additional services can include refining scope of work/cost estimate, engineering support for subrogation or legal action (including expert witness requests), design for temporary modifications to get business operational, as well as design and construction support.
Q. You also provide industrial architecture services. Describe what that entails and why this isn’t necessarily provided by an architect?
A. In chemical, process, and industrial environments, code review and compliance requirements can get complex due to process operations, building use, material characteristics, material handling, material storage (pile size and heights), fire protection systems, site conditions, setbacks, and other related conditions. Industrial architects have the experience and resources available to complete the complex code reviews necessary to design and permit these facilities. Traditional architects typically do not have the experience, expertise, or the comfort level necessary to complete this type of work.
Q. What is process safety management (PSM) and what types of plants are required to comply?
A. Process Safety Management is an OSHA standard which mainly applies to manufacturing industries — particularly those pertaining to chemicals, transportation equipment, and fabricated metal products. Other affected sectors include natural gas liquids; farm product warehousing; electric, gas, and sanitary services; and wholesale trade. It also applies to pyrotechnics and explosives manufacturers covered under other OSHA rules and has special provisions for contractors working in covered facilities. In each industry, PSM applies to those companies that deal with any of more than 130 specific toxic and reactive chemicals in listed quantities; it also includes flammable liquids and gases in quantities of 10,000 pounds (4,535.9 Kg) or more.
The applicable standards include OSHA 1910.109 – Explosives and Blasting Agents and OSHA 1910.119 – Process Safety Management of Highly Hazardous Chemicals
The requirements to comply with these standards are extensive and involve a significant effort to initially develop the documentation and continually update and keep current. The requirements include process safety information (extensive process information including PFD’s and P&ID’s), process hazard analysis (PHA), operating procedures, employee participation, training (with documentation), contractor requirements, pre-start-up safety review (PSSR), mechanical integrity, hot work permit, management of change (MOC), incident investigation, emergency planning and response, and compliance audits. We have assisted clients with many of these requirements.
Q. Why do plants need to have pressure relief device calculations and documentation, and how extensive of a process is this?
A. Pressure safety devices may include conservation/emergency vents for tanks or vessels, rupture disks, pressure safety valves, and more. The pressure relief devices are a critical and integral part of the safety systems included in a chemical or process plant. There are several reasons for having the relief system design/design basis for each device, including device rating, material requirements, defined setpoints, testing, instrument maintenance, replacement, and regulatory compliance (process safety management). Many process plants are required to have these calculations on file to meet audit requirements.
Pressure safety devices are sized based on worst-case conditions, which can include fire case, blocked flow or thermal expansion, and involve liquids, gases, or mixed flow conditions. Designing the pressure safety device during the design of a plant is an integral part of the engineering process. Defining the design basis and performing calculations on existing devices in an existing plant can be much more complicated as it requires the complete understanding of the process, fluid or gas characteristics, safety philosophy for the plant, the inlet/outlet pipe sizes, piping length/configuration, and more. The work typically involves review of accurate piping and instrument diagrams, device tag information, device specifications, fieldwork, and calculations. The extent of work can vary based on the complexity of the process and sizing requirements for the device. We have done calculations and documentation for entire plants, which can add up to hundreds of relief devices.
Proper sizing and selection are critical for the plant, equipment, piping, and operator safety.
For more information on process engineering, contact D. Kevin Bingel, P.E., and Dale Niethammer, P.E.