MedPharm Iowa: Teamwork + Expertise = Completion in 1 Year
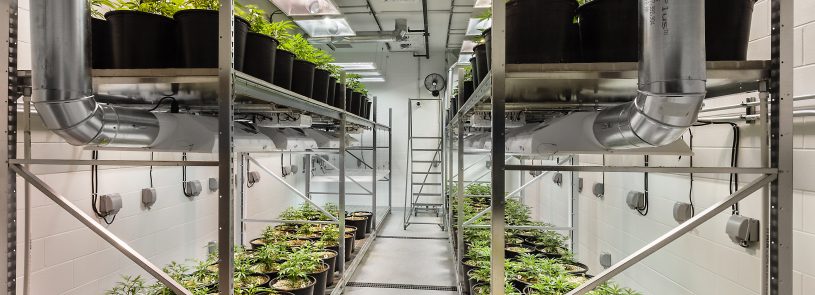
By Luke Streit, PE
Getting a complex renovation project from design to operation in one year is no simple task. But that’s what the design and construction team was asked to accomplish for MedPharm, Iowa’s first medical marijuana manufacturing facility. I served as project manager for IMEG, which provided MEP, fire protection, and technology/security design for the facility. Our work with the project architects began as soon as MedPharm was granted a license by the State of Iowa in late November 2017, allowing them to manufacture three types of medical marijuana products to be sold at the state’s five licensed dispensaries. The license also required that the company have the products ready to dispense by Dec. 1, 2018 – giving us 12 months to complete the project. Besides our technical abilities, two critical differentiators helped our team meet the state-mandated deadline: our local presence and our experience and familiarity with each other and the owner. Our same team had recently worked on the design for the new world headquarters of Des Moines-based Kemin Industries, MedPharm’s parent company. Kemin knew we understood the firm’s procedures and thought processes and could get up to speed quickly on a new project. Our local presence provided us with experience working with the City of Des Moines building department and made it easy for us to meet with department officials prior to the receipt of the license. This ensured we understood the permitting and inspection processes as well as the code requirements that would come into play with the existing building – a 1960s-era freight distribution warehouse near the Kemin campus. We also were able to investigate the existing conditions of the building. At the time of design, medical marijuana processing was a new type of project for the team, so Kemin arranged for us to visit a similar facility, MedPharm Colorado, in Denver. We toured that facility and met with the users to gain a better understanding of the highly secure, strictly controlled scientific process. Early design and planning Our proactive investigations saved us valuable time and allowed us to hit the ground running once the project was given the green light by the state. We spent the first month meeting with the owner, user groups, and contractors to work through the tight project budget and schedule and conduct master planning-type exercises to determine not only what needed to be operational on day one, but also how to provide flexibility for future growth and expansion. We then conducted several rounds of conceptual design, aided by an architectural firm with expertise on the unique process equipment requirements. Using rendering software, we turned our Revit model into a 3D virtual walkthrough to help the owner see, understand, and approve the final design. The project delivery was a highly collaborative effort between the design team, the general contractor, the fire protection and security systems subcontractors, and the mechanical and electrical contractor. The trade contractors also provided prefabricated assemblies, which were critical in meeting the timeline. We peer reviewed each other’s work throughout the project and worked closely with the vendors to determine the utility requirements of all equipment. To allow MedPharm the time it needed to grow, harvest, process, and package its first batch of product by the state’s deadline, design and construction were phased, with the most critical and time–sensitive spaces brought online first. Phase 1 Design and construction for phase 1 consisted of office and support spaces, core mechanical, electrical, and utility spaces, and the “mother grow room” and propagation chamber for the genetic stock of all the plants. These prefabricated rooms were delivered to the site and then connected to all utilities, including reverse osmosis (RO) water. The mother chamber was operational by February, allowing MedPharm to begin growing breeding stock while the next two phases were being designed and built. All infrastructure that would be needed for phases 2 and 3 also was installed during phase 1. This included all AHUs, chillers, electrical gear, emergency generator, water service, sanitary sewer, and natural gas. The portion of the fire protection system serving phase 1 also was operational, allowing the city to issue a certificate of occupancy to MedPharm so that it could begin operations. Phase 2 The facility’s vegetation and flower rooms and related support spaces were designed and constructed in phase 2 and came online in June – in time to receive the first crop of plants from the mother grow chamber. This phase – which connected each room to the building infrastructure installed during phase 1 – required several design iterations for grow lighting specifications, lighting layout, as well as HVAC systems – primarily cooling and dehumidification. Lighting, temperature, and humidity are critical for these rooms; any deviation from acceptable levels puts the entire crop at risk for lower yields and/or disease, costing the owner in wasted resources, time, and revenue. Thus, sensors constantly monitor room conditions and all mechanical and electrical systems have redundancy. A carbon dioxide enrichment system was also designed and utilized for the grow rooms. Phase 3 The final stage of the project provided design and construction of the extraction, quality control, and packaging spaces. These areas are essentially a lab space in which employees separate the oils from the dry cannabis matter and package the final products, which come in the form of creams, pills, and drops. This stage required attention to all utility and safety requirements for the processing and lab equipment, along with close coordination with the owner and equipment manufacturers. With the spaces and lab and process equipment fully defined, the design team reconciled the actual Phase 3 HVAC loads with the system assumptions made early in the project. IMEG collaborated with the contractor to ensure the final HVAC design remained within the project budget and schedule. Up and running MedPharm’s $10 million, 15,000-square-foot manufacturing facility was fully complete and operational by November 2018 and the company began selling its product later that month from its dispensaries in Windsor Heights and Sioux City. The firm produces three products with ranging levels of cannabidiol, commonly referred to as CBD, and tetrahydrocannabinol, commonly referred to as THC. CBD is a non-intoxicating cannabinoid that can help people with seizures or Crohn’s and Parkinson’s diseases; THC is the psychoactive cannabinoid that can help people manage pain associated with cancers, Lou Gehrig’s disease, multiple sclerosis, and terminal illnesses. The fast-track project was intense but rewarding, made possible by the skills of our design and construction teams and everyone’s willingness to work together from start to finish to ensure project success for the owner. |