Robust, accessible building documents reduce risk during renovations
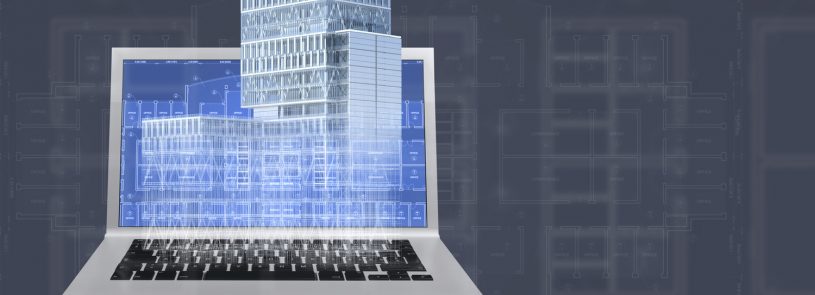
By Kelly Altes
I once attended a seminar titled “Bridging the Gap between Construction Closeout and Facilities” at an IFMA – World Workplace Conference. One of the key risk mitigation take-aways was the management and accessibility of closeout and current documentation – information that is so critical to future projects at a facility.
As a design firm, we are often asked to turn over closeout documentation to our clients. Some of the owners have a document management system in place, while others store the information we provide on a shared drive where only a few people in the organization will ever refer to it again.
Keeping up-to-date plans (not only architectural, but MEP, structural, and civil) can save many future headaches. Unforeseen conditions cause the most change orders during construction renovation projects – millions of dollars and precious time are wasted because of poor initial information. Documenting existing conditions helps avoid this.
Key problems facilities leaders face in the management of facility documentation include:
- Individuals with years of institutional knowledge in facilities are retiring and the “documentation” about the facilities is stuck in the brains of those retirees.
- During an emergency situation, O&M manuals with equipment information and paper plans that show where shut–off valves are located are useless because it takes too long to access them.
- When a life safety situation arises, the EMS personnel responding don’t know your building or campus layout. Not having mobile access to camera surveillance or the ability to send a text message with a specific plan view location could cost lives because of the lost time and chaos.
- Facilities may have a nice set of existing drawings from the initial facility build, but any renovations that may have happened over time are scattered puzzle pieces. MEP designers often spend an inordinate amount of time doing field take–off to document existing conditions. Civil engineers may have to request potholing during the design process to dig up what is below ground for verifications, and structural engineers may want materials testing, X-ray, or invasive demo to determine material properties.
- The gap between technology for construction implementation and facilities management is large. Owners are not investing the same amount of money in facility management software and current documentation as design and construction firms. Sometimes owners are not sure what new technologies are available to help them manage their new facility. Sometimes they have no real day-to-day use for BIM models or other documentation from the construction process.
Documentation management software can resolve these issues. For the best outcome, be sure your software solutions enable you to:
- Put your facility documentation in a central digital location in a secure cloud, where it can be accessed from an app on a phone so it can be an important component to changing a catastrophic emergency into a small, manageable issue. Make sure the software permissions are manageable for security purposes.
- Properly document campus maps with building numbers identified. The same software should have the ability to note on floor plans, at each level of the building, the locations where specific renovations and improvements have occurred.
- Tag your equipment with QR codes that will connect via an app to O&Ms, critical equipment maintenance information, and plan locations.
- Link to details and search/filter data on plan sets, schedules, and O&Ms. Each equipment or safety asset needs tags for physical location and maintenance identification.
- Provide easy and simple ways for maintenance staff to document “new discoveries” or changes they make in real time by taking a photo and connecting that photo to a plan set.
- Accommodate 3D photo documentation during construction. Use software that will stitch these photos together, creating a “dollhouse” view of what is behind the walls or in your slabs at specific points in time. Connect these scans with your building management software for easy maintenance access.
- Keep it simple! Any software that is overly complicated won’t be widely accepted or used. To encourage adoption, offer team members incentives or recognition for documenting changes.
As a disclaimer, I am always skeptical about new software. Vendors show you the best examples that are seamless and without flaws – but when you begin to use the software you discover the inadequacies. However, if you are vigilant and do your homework, you can find software with significant value.
Finding the right product for your facility could provide real ROI to leadership through software implementation that better manages building documentation for both future improvements and managing emergency situations.