Site selection due diligence: Ensure utilities meet project needs
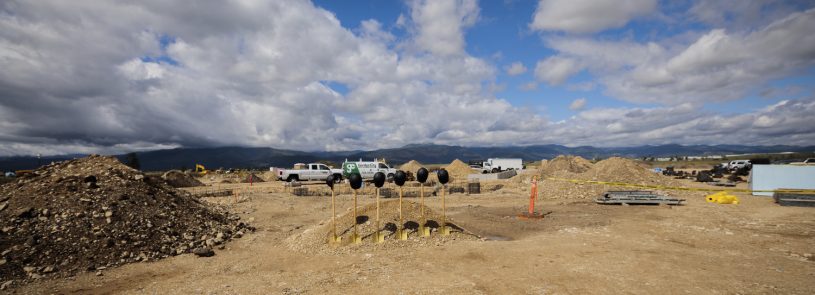
By Joel DeHaven
Businesses spend a lot of time and effort looking for the right property for their operations. This search often includes important factors like access to freeways or other transportation; ample space for offices, warehousing, and production; and lease or purchase costs. Often, however, the availability of utilities can be overlooked. This can happen due to unfamiliarity with system design requirements or just an assumption that the utility companies can provide whatever is needed.
Questions like, “Is there natural gas available?” are asked, when the real question may need to be, “How much natural gas capacity is the building designed for?”
Manufacturing or processing facilities can consume large amounts of power, water, and natural gas, and these utilities may not be available in the quantities needed without expensive and time-consuming upgrades by the serving utility companies. In some cases, this can involve miles of piping or electrical feeders to bring properly sized lines to the property.
These upgrades are further compounded in the current construction climate due to delays in procuring equipment and materials. Even large purchasers of equipment, like utility companies, are finding that equipment delivery may take several months to more than a year due to supply chain backlogs.
While the reality of supply chain issues and utility company limitations are unavoidable, working with a knowledgeable engineering consultant can be an important part of the due diligence process for a building or site selection. Knowing about utility limitations can allow businesses to consider other site options, modify lease or purchase terms, or modify project schedules to accommodate required utility upgrades. Preliminary engineering evaluation can also allow businesses to make process decisions that may better suit the utilities that are available.