Use Measurement & Verification to maximize building performance
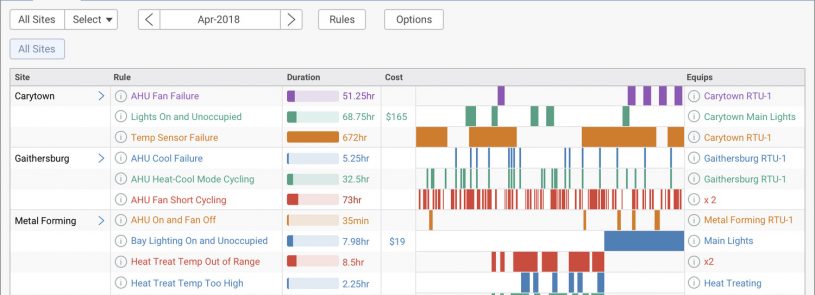
By Lincoln Pearce
Every engineer and owner wants their building performance to be what it was designed to be. But numerous factors – from faulty equipment to user behavior – can cause subpar building performance in even the most efficiently designed buildings. An effective way to reduce this risk and optimize your facility’s energy use post-construction is through measurement and verification (M&V).
M&V is the process of measuring and analyzing your facility’s energy use data after a project is completed to see if your facility is operating as it should. The earlier your M&V plan is integrated in project development, the greater the potential that energy performance can be optimized.
Key components of an M&V plan should include:
- Establishing the building energy use target during design through modeling and benchmarking
- Including energy metering and reporting of data in the project design
- Data gathering once occupancy has begun
- Evaluating and calibrating the data and comparing to the design target
- Identifying causes for unexpected or less than optimal performance
- Implementing corrective measures
- Continued monitoring to ensure the corrections are effective
Not only can M&V detect when a building is not meeting its energy goal, the data gathered through metering and sub-metering can help facility managers more easily pinpoint the system or systems that are causing the problem(s).
A good example: When energy reports revealed that the recently renovated Marston Hall at Iowa State University was using more energy than our original LEED energy modeling analysis had predicted, we performed a LEED M&V analysis to determine the cause. The analysis revealed that a steam pre-heat coil control valve had been commanded open 100 percent at all times, inflating both chilled water and steam energy use unnecessarily. The university used this finding to correct the control valve operation and they continue to monitor the building’s energy use to ensure the problem is resolved.
Had M&V not been in place, the issue could have gone undiscovered indefinitely – reducing the university’s return on its investment in Marston Hall’s high-performance technology and causing substantial additional energy costs. Based on the M&V findings, the correction of the steam valve operation avoids about $24,000 annually in unnecessary energy use.
So, if you want to be able to keep tabs on your building’s energy consumption, implementing an M&V process as part of your design and operations is a relatively inexpensive way to ensure long-term savings.
Like the saying goes, you can’t manage what you don’t measure.