Verifying access to power capacity on manufacturing sites amid strain on the grid (Podcast Included)
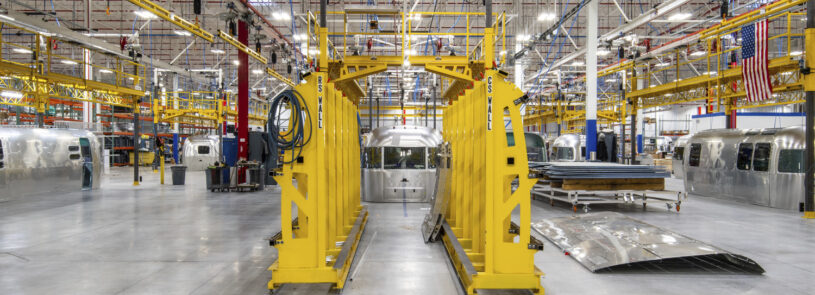
By Mike Walsh
As the U.S. manufacturing sector continues to rebound and modernize, it faces a growing challenge: ensuring reliable access to power amid increasing strain on the national grid. The following explores why proactively verifying access to power is critical for manufacturers, the factors contributing to grid strain, and how forward-thinking companies can navigate this challenge.
Rising energy demands and grid strain
The U.S. power grid is under significant stress, facing a combination of factors that complicate energy distribution. According to the U.S. Energy Information Administration, the country’s total electricity consumption has been steadily rising, driven by population growth, increasing conversion from natural gas to electrical appliances and building systems, and the expansion of energy-intensive industries. At the same time, the grid is also contending with more extreme weather events, aging infrastructure, and the growing shift toward renewable energy sources, which are intermittent by nature.
For manufacturing sites, especially those relying on energy-intensive processes, this increasing strain on the power grid can pose serious risks. Fluctuations in power supply or unplanned outages can lead to production delays, equipment damage, and financial losses.
Verification of power capacity
As manufacturing processes become more automated and reliant on precision machinery, an uninterrupted, stable, and sufficient power supply is essential. Manufacturing facilities need to ensure that their power access aligns with the required load demands of their equipment. This includes:
- Peak demand: Manufacturers must verify that their energy contracts cover both the baseline and peak energy demands of their facility. Inadequate power capacity can result in forced downtimes or even equipment failures during high-demand periods.
- Infrastructure limitations: Not all regions have the infrastructure to support sudden increases in energy demand. Verifying power capacity includes understanding local utility grids and potential bottlenecks in transmission lines, transformers, and substations.
- Energy efficiency goals: With sustainability goals becoming increasingly important, manufacturers are also under pressure to adopt energy-efficient practices and leverage renewable energy sources. Ensuring that the infrastructure can integrate green energy solutions, such as solar panels or wind turbines, is essential to avoid capacity issues.
Consequences of unchecked power access
Manufacturing plants that fail to verify power access may experience:
- Production downtime: Power outages, even brief ones, can lead to substantial production delays. A single day of downtime in a large plant can result in losses of thousands—or even millions—of dollars, depending on the industry and scale of operations.
- Operational inefficiencies: Insufficient or unreliable power supply can cause machinery to operate erratically, leading to inefficiencies and increased wear and tear on equipment. This can shorten the lifespan of critical machinery, increase maintenance costs, and lead to costly repairs.
- Compliance risks: Many manufacturers must meet stringent regulations on energy use, emissions, and waste. Insufficient power supply, especially if it forces a facility to rely on backup generators or less efficient processes, could result in non-compliance, triggering fines and reputational damage.
- Financial strain: Energy is one of the largest operational costs for many manufacturers. Unpredictable energy access could force manufacturers to pay for expensive backup power options, further increasing operational costs. Additionally, increased reliance on fossil-fuel-powered backup generators can drive up carbon footprints and operating expenses.
Strategies for verifying power access
To mitigate risks, manufacturers must adopt comprehensive strategies to verify and manage their access to power capacity, such as:
- Conducting power assessments: Regularly assessing both current and future power needs, particularly as production demands shift or new technologies are integrated, is essential. A detailed load analysis should account for all machinery, HVAC systems, lighting, and future growth potential.
- Engaging with local utility providers: Building relationships with local utility providers is key. Manufacturers should communicate their energy needs, potential growth, and backup power plans with utility providers to ensure the grid can accommodate their demands. Some utilities may even offer incentives for energy efficiency or load-shifting measures, such as demand response programs.
- Backup power planning: While backup generators are a common solution, manufacturers should ensure they are properly sized, regularly maintained, and capable of covering peak demand without causing additional strain on the grid. Backup power systems should be tested frequently to ensure they can be activated quickly in the event of an outage.
- Investing in energy storage: The rise of energy storage solutions—such as batteries—has given manufacturers an option to buffer against power supply interruptions. By storing excess energy during periods of low demand, manufacturers can release this stored power during high-demand periods, reducing their reliance on the grid and minimizing operational risks.
- Embracing renewable energy: To offset grid reliance, many manufacturers are turning to renewable energy sources. Solar, wind, and geothermal systems can be integrated into manufacturing sites, offering a more sustainable and reliable alternative to traditional energy sources. These solutions also help future-proof operations as energy demands evolve and regulatory frameworks tighten.
Looking to the future
As the U.S. grid continues to evolve with the increased integration of renewable energy sources, manufacturers must remain agile and forward-thinking. The shift to cleaner energy sources is essential for addressing climate change, but it will also require manufacturers to adjust to more dynamic energy pricing, potential grid instability, and challenges related to energy storage and transmission.
To thrive in this changing landscape, manufacturers will need to not only verify their access to power but also engage in long-term energy planning that aligns with both business needs and environmental objectives.
Listen to the podcast: