Creamery Renovation and Addition
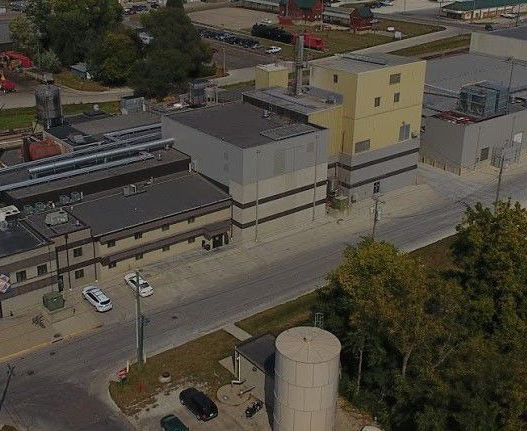
IMEG provided mechanical and electrical engineering design services for the HVAC, plumbing, process piping, power, and lighting systems for Wapsie Valley Creamery’s new cheese packing line. Our team worked with the owner, architect, and the process equipment vendor to assure the project would meet the owners requirements.
Key system designs included variable air volume (VAV) air handling system with VAV boxes with hot water reheat, custom air handling unit (AHU) with indirect gas-fired pre-heat, glycol water cooling coil, and hot water re-heat coil to provide for space temperature and humidity control. The AHU is 45,000 cfm with approximately 165 tons of cooling capacity and two (one redundant) 1,500,000 BTUh natural gas fired boilers provide hot water for heating.
Innovative solutions to meet owner requirements included:
- The owner wanted to resolve negative air pressure issues in the current plant so designs included increasing outside air capabilities of the AHU to accommodate the negative air pressure issues.
- The owner wanted the ability to control humidity in the processing and packaging areas. To accomodate this, cooling coils were sized to lower coil temperature which will remove moisture from the air stream, and then a hot water reheat coil is utilized to reheat the air to maintain space temperature.
- When Wapsie Valley Creamery employees goes into cleaning mode, clouds of vapor flood the room. The building air handling unit is controlled to go to virtually 100% outside are during the cleaning time period to exhaust the moisture generated during clean up and
still maintain building temperature and room pressure relationships. - The project was fast-tracked, with building construction proceeding before all systems were designed. Process equipment design was constantly changing, requiring numerous design and drawing revisions. The architect and IMEG produced their design using REVIT, and models were continually updated to reflect changes and to assist in construction coordination.