New Headquarters and Manufacturing Building
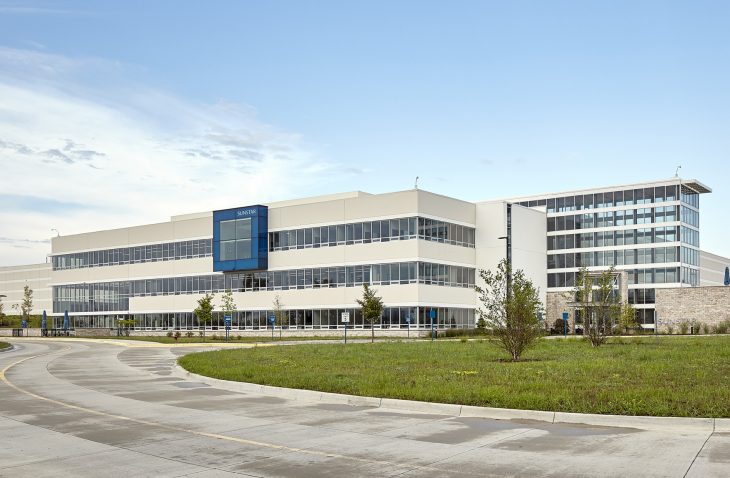
IMEG provided structural engineering design services for SunStar America’s new, three-story office headquarters and single-story manufacturing facility. The headquarters consists of a cafeteria, training classrooms, offices, and gathering and executive spaces.
The goal of the structural design for the office space was to bring the outdoors inside. The building’s gallery space provides a gathering space and a visual link between the office and manufacturing spaces, using glass expanses and minimalist structure. The steel framing throughout the gallery is designed to a shallow depth so the wood slat ceiling sits on the bottom flanges, creating a clean look. Engineers maintained the same depth structure throughout the gallery space while addressing vibration concerns, large openings for vertical circulation, and bracing the adjacent basement wall construction.
The manufacturing facility design provided 32-foot clear height and an unobstructed plan layout, except for the main building columns. Additionally, the slab on grade is a high performance design. Ductilcrete was selected to provide a thinner slab, and it enables the quantity and spacing of control joints to be substantially increased, which will decrease long-term maintenance issues.
This project had three main challenges:
- The facility was built into a hillside, which meant taking advantage of the natural topography was a primary concern. To accommodate this, the headquarters entry level is a story below the manufacturing level. The different floor levels created the need for basement or retaining walls that needed to withstand the manufacturing floor and soil pressures.
- Early structural packages always pose a challenge to the design team, in addition to making sure the owner’s needs are met. To help achieve a quick schedule, load-bearing precast wall panels and joist framing were used to construct the manufacturing facility. The headquarters consists of composite steel beam framing and steel lateral moment frames. The steel framing provided the best structure to support the cladding, which included wide/continuous expanses of glass.
- The process engineering requirements were relatively unknown during design of the building superstructure. As those needs developed, the design team reacted by checking the structure for a 30-ton bridge crane, designing mezzanine areas for dry and wet manufacturing along with shipping/packing spaces, and designing screen wall framing and pit slabs around the tank farm.