Renovation and Expansion of Energy Center
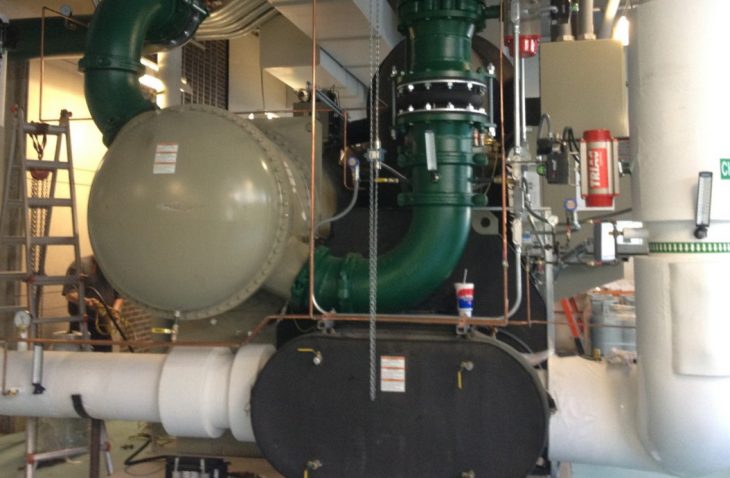
IMEG provided mechanical, plumbing, and electrical engineering services for the VA campus in Cleveland to design and construct renovation of a 5,200-sf energy center. The renovated plant was sized to accommodate the existing building cooling demand as well as demand of new additions which increased the hospital area from 1,000,000-sf to 1,400,000-sf.
Chilled water system: The new chilled water system will utilize centrifugal electric chillers with open-cell cooling towers. The plant includes (5) 1200-ton chillers with matching cooling towers and provide N+1 redundancy for the entire hospital. The chilled water will be delivered via (6) 2400 GPM variable-flow pumps configured in a variable-primary configuration. The cooling towers will be provided with (6) 3600 GPM pumps. This equipment will be placed on emergency power to ensure chilled water service during power outage. Due to problems with the original controls the chillers were manually switch from online to off-line. A new sequence of operations was designed to correct problem of the past and accommodate the new equipment. This sequence included multiple sessions with the controls contractors, VA energy engineer, VA supervision and most importantly the experience plant operators.
An upgraded refrigerant monitoring system generates audible and visual alarms and provides exhaust through a dedicated exhaust fan. A solids separator was added to reduce dirt in the condensing water system. Ultrasonic flow meters were added for energy calculations and more precise control.
Process chilled water system: An independent process chilled water system was designed to serve process heat loads within the hospital such as radiology equipment and data rooms. This system will provide chilled water year-round and allow shutdown of the central plant chillers when outside air falls below 45 degrees. This system also replaced the use of once through domestic cold water for cooling. The new process chilled water system will utilize water cooled rotary electric chillers with fluid coolers and a free cooling heat exchanger. The plant includes (2) 250-ton chillers, matching fluid coolers, and a free cooling heat exchanger will provide N+1 redundancy for the process loads in the entire hospital. The chilled water will be delivered via (2) 480 GPM variable-flow pumps configured in a variable-primary configuration. This equipment will be placed on emergency power to ensure chilled water service during power outage.
Generator power: A 2,000 KW emergency generator was provided as part of this project. New fuel oil pumping systems was provided that will transfer fuel oil from the existing underground storage tanks (adjacent to the energy center) to the generator belly tank. This was added to the four existing generators (2) 1000 KW and (2) 1500 KW. Provided new 3000kVA, 11.4kV:480/277V electric substation for new chillers. Added switchgear to provide 3000 amp, 480/277 volt -3 phase connection to the existing paralleling plant.
This additional 2000 KW generator added the chilled water system to the emergency power system and allow for the generators and chillers to be utilized for a peak load shedding program encourage by the utility company. This program provided a new revenue source for the hospital.