Critical lift cranes require additional specs and safety measures
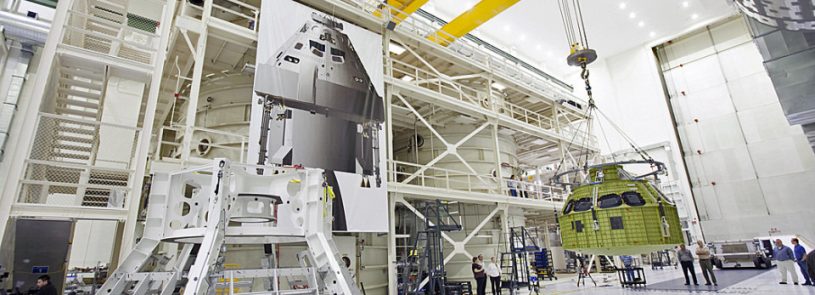
By Edwin Dean
Critical lift cranes are used to handle “critical” hardware; in the aerospace industry, this could include high-value components like spacecraft or satellites (in excess of $100 millions) or components that contain hazardous or highly toxic materials (hypergolic fuels).
The procurement, installation, and operation of critical lift cranes requires the definition of additional requirements above and beyond the national consensus standards (i.e., OSHA 1910.179, ASME B30 series, CMAA 70/74) typically specified for a standard commercial crane. Significant recommended requirements that must be specified for all critical lift cranes include:
- The crane should be specified for at least CMAA 70 Class D equivalent service
- For the hook, shank, shank threads, nut (including nut threads), or pinned shank hooks, the attachment pin should undergo volumetric and surface NDE prior to any load testing. After successful initial NDE, the hook and nut assembly should be proof load tested prior to installation on the crane, then undergo additional volumetric and surface NDE inspections
- Wire rope should be attached to the crane by a rope termination method that develops 100 percent of the rope strength (with the exception of rope-to-drum attachments). New wire rope terminations should be volumetrically and surface NDE inspected and certified before installation on the crane
- Hoists should be dual reeved with all load lines terminated at an equalizer bar and drum(s). Hoists should be reeved with one right-lay rope and one left-lay rope to cancel the load block rotation tendency. At least two wraps of the rope should remain on the drum at the lower limit of lift. Hoists should be equipped with a means (such as a level-wind device) for preventing the load line from coming out of the drum groove and overwrapping itself on the drum
- Hoists should be equipped with two limit switches in the “up” direction to prevent “two blocking” and one limit switch in the “down” direction to prevent a slack rope condition
- Hoists should be designed with an adjustable hoist overload detection device
- Hoists should have three independent braking systems: A load control braking system, a load holding brake system, and an emergency braking system on the hoist drum. All braking systems should each be capable of braking and holding at least 150 percent of torque exerted by a full rated load on the hook. Each braking system should be capable of being tested independently in place
- Hoists should be provided with a speed-sensing device. If the hoist speed exceeds 110 percent of its rated speed, all braking systems and audio and visual warning devices should be activated
- Hoists should be equipped with an un-commanded motion sensor to detect differences in speed ratio between the drum and the hoist motor. If un-commanded motion is sensed, all braking systems and audio and visual warning devices should be activated
- A torque-proving system should be provided for all hoist drives and motors to ensure that the hoist holding brakes are not released until the motor has been verified for its ability to energize
- Hoists should have an emergency lowering capability to safely lower a full rated load in the event of a power failure or hoist drive mechanism malfunction
- A Single Failure Point (SFP) Analysis and Failure Modes Effects Criticality Analysis (FMECA) should be provided. The FMECA identifies failure conditions that could result in personnel injury, loss of load, or damage to critical hardware and should encompass the complete power and control circuitry as well as the load path from hook to structure
- Manufacturer data package should include all NDE test reports for the hook/nut, wire rope termination fittings, and all identified SFPs (components and welds)
- Crane owner should conduct an SFP Analysis on the crane support structure (i.e., runway rail and building attachments) along with NDE testing of any identified SFPs (components and welds). In addition, 10 percent of non-SFP welds on crane support structures should undergo NDE inspection before and after crane proof load.
- Crane owner should compile the following documentation:
a. Crane specifications/procurement documentation
b. All SFP Analyses
c. FMECA
d. Stress analysis (calculations) for crane and crane support structures
e. Available CAD output (drawings)
f. Initial NDE test reports/documentation
g. Software test plans and results (if applicable)
h. Initial test plans/procedures and results.
i. Certificate of conformance to specifications
j. Recurring NDE plan with special emphasis on identified SFPs
k. Recurring test plans/procedures
It is imperative that these additional requirements be addressed in the initial procurement documentation prior to initiating a contract, since it will be difficult or impossible to incorporate them later into a typical commercial crane without substantial modifications and significant cost.